(303)
758-2728
|
Home
> Mechanical
Seals Operating Principles > Fluid
Leakage
Mechanical Seals
Operating Principles
The
fluid in the pump and seal area
Key
Point:
the fluid contacts the seal faces and other parts in wide open areas,
in very small gaps and at the exit of the seal faces. Pressure and temperature
of the fluid will depend on its location and determine its respective
state, i.e. liquid, gaseous, solid or a mixture.
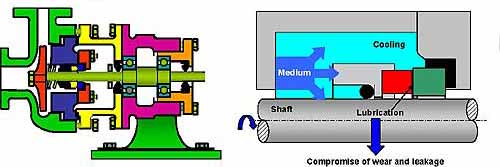
A
few facts about the leakage (and wear) behavior of contacting mechanical
seals:
- It is
essential for proper lubrication and wear of the faces.
- Normal
leak rates range between immeasurably small to steady drips or temporary
to even small steams. Some seals leak some of the time, some seals never
leak (measurably), and some leak all the time. Leakage patterns can
be constant, progressive or erratic in nature.
- It can
be in liquid, gaseous and/or solid state.
- Successful
contacting seals tend to have very low wear rates and low leakage rates.
- Some forms
of contact is necessary for low leakage rates. Non-contacting or “full
lift off” seals (hydrostatic or hydrodynamic tend to have visible,
sizeably larger leakage rates.
- The large
majority of mechanical seals never wear out and are removed from service
for some other reason.
- Seal failures
occur for a wide range of reasons. Some failures occur as an
interaction with the tribology of the interface.
Next:
Effective
forces in a mechanical seal
We are located in the Denver Technological
Center in a suburb of Denver, Colorado
©1997-2017, Problem Solving Products, Inc.
Website Map | Privacy Statement
| Terms of Use
|